A properly-maintained C300 heat exchanger is the cornerstone of thermal performance in commercial approaches. Known for its durability and high overall performance, the C300 model is widely used in sectors like chemical processing, energy generation, and HVAC systems. Despite its strong design, this system requires ordinary preservation to continue running at height stages. The operational environment, kind of fluids processed, and integration with structures like vacuum pumps all affect the frequency and approach of renovation. By following established practices, operators can maximize efficiency, save you unplanned downtime, and enlarge the lifespan of this important system.
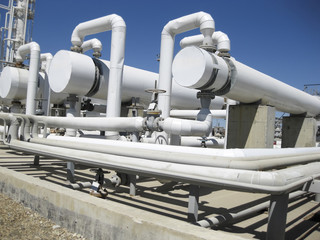
Understanding Common Maintenance Requirements
Importance of Regular Inspection
Routine inspections are the muse of effective heat exchanger protection. Regular visible tests help discover surface corrosion, leaks, unusual noises, or misalignment of mechanical connections. These symptoms regularly factor to deeper problems that might increase into main disasters if disregarded. By establishing a steady inspection schedule, facilities can catch early signs and symptoms of harm, which can be simpler and much less expensive to restore.
Routine monitoring of temperature differentials and pressure drops across the unit also can provide essential perception into the exchanger’s situation. A narrowing temperature hole or rising stress drop commonly indicates fouling or waft regulations, which could degrade overall performance through the years.
Monitoring Performance Metrics
Operators ought to closely screen key performance signs inclusive of warmness switch efficiency, outlet temperatures, and float rates. These information points can reveal diffused performance changes, signaling the want for cleaning or aspect replacement. For systems that operate along vacuum pumps, it’s miles important to also study any stress fluctuations which could effect thermal balance or cause condensation within the exchanger.
Cleaning Techniques for Extended Service Life
When to Clean the Heat Exchanger
Cleaning frequency relies upon at the sort of fluid passing thru the unit and the machine’s running situations. If the fluids are high in particulates, minerals, or organic count, fouling can arise extra rapidly. Visual inspections and changes in drift or warmness switch efficiency help decide the best cleaning periods. Waiting too long between cleanings can motive permanent scaling or corrosion, making preservation extra hard and steeply-priced.
Chemical cleaning is suggested for mineral or organic buildup that cannot be removed via simple flushing. On the opposite hand, mechanical cleaning is powerful for sticky or hardened deposits. It’s essential to apply substances and strategies that won’t damage the inner surfaces or gaskets of the C300 warmth exchanger.
Cleaning In-Place (CIP) Systems
Many commercial setups integrate Clean-In-Place systems that allow for inner washing without dismantling the exchanger. This method minimizes machine downtime and labor even as improving maintenance consistency. CIP involves the move of cleansing dealers thru the exchanger at controlled pressures and temperatures to dissolve contaminants. The use of non-abrasive, chemically compatible fluids ensures that the device is wiped clean with out causing harm to its components.
Preventing Fouling and Scaling
Water Quality Management
One of the number one reasons of fouling in warmth exchangers is terrible water pleasant. High stages of calcium, magnesium, or biological rely can cause scale and biofilm accumulation. Treating method water with filtration, softening, or biocides can greatly lessen the probability of such problems. Operators should often check water first-rate and alter remedy protocols as a result.
For systems the usage of vacuum pumps, moisture condensation from vapors may introduce contaminants into the heat exchanger. Implementing condensate separation or vapor filtration upstream can decrease this hazard and preserve the exchanger’s interior condition.
System Design Enhancements
Design considerations such as fluid speed, waft course, and surface configuration play a vital role in fouling prevention. Ensuring optimal turbulence inside the exchanger reduces the hazard of particle agreement. Installing monitoring sensors at strategic points inside the machine enables to track temperature profiles and discover areas where fouling is probably to begin.
Corrosion Prevention Strategies
Material Compatibility
Corrosion is one of the maximum unfavourable issues for heat exchangers. It can compromise structural integrity, motive leaks, and reduce performance. Using materials which are well suited with the working fluids is critical in preventing chemical reactions that purpose corrosion. The C300 warmth exchanger regularly comes in chrome steel and different corrosion-resistant alloys, however even those want right tracking.
When exposed to competitive fluids or environments, it is able to be useful to apply specialised coatings or linings to provide an additional barrier in opposition to corrosive agents. These coatings ought to be inspected periodically to make certain they remain intact and effective.
Environmental Controls
Ambient factors which includes temperature, humidity, and publicity to commercial chemical compounds also can result in outside corrosion. Ensuring right air flow, shielding the exchanger from chemical fumes, and coping with condensation can help preserve the outdoors surfaces. Storage practices also are essential—if the exchanger is offline for extended periods, it need to be tired, dried, and protected in opposition to environmental publicity.
Gasket and Seal Maintenance
Detecting Wear and Tear
Gaskets and seals are small additives, however their failure can result in foremost overall performance issues. They are frequently the first components to wear down because of thermal biking, pressure variations, and chemical exposure. A visual inspection may additionally display hardening, cracking, or deformation. Any signs of leakage across the gasket location recommend that it’s time for a substitute.
Gasket put on is more not unusual in structures that frequently start and forestall or experience speedy adjustments in temperature and strain. Therefore, it’s far crucial to use gaskets which can be specifically designed for the conditions present in your heat change utility.
Replacement and Installation Best Practices
When changing gaskets, it’s crucial to apply models that match the manufacturer’s specifications in phrases of size, cloth, and temperature rating. During installation, surfaces ought to be easy and freed from debris to make sure right sealing. Over-tightening bolts or uneven torque distribution can purpose damage to the gasket or deform the metallic plates. Consistent methods and torque tools have to be used to hold right compression throughout the whole sealing surface.
Long-Term Storage and Downtime Procedures
Protecting Idle Equipment
When the C300 heat exchanger isn’t always in use for an prolonged period, it desires to be covered in opposition to corrosion and mechanical put on. The exchanger should be completely drained and flushed to cast off residual fluids. Dry air or nitrogen purging can prevent moisture accumulation within the unit.
The exchanger have to also be covered or stored in a temperature-controlled surroundings. Applying anti-corrosion coatings or desiccants inside the unit can provide similarly protection. These measures keep the system’s circumstance and reduce reconditioning time when the exchanger is again to carrier.
Documentation and Readiness Testing
Before bringing an idle warmth exchanger back into operation, it’s essential to check for integrity. This includes pressure testing, thermal biking, and an intensive inspection of gaskets and surfaces. Keeping a detailed log of storage conditions and renovation activities allows make certain that the exchanger is ready for service with none surprises.
Training and Operator Awareness
Routine Training Programs
Even the exceptional-designed upkeep plan will fail if operators are not skilled to put in force it properly. Routine education periods need to recognition on spotting signs of wear and tear, interpreting performance facts, and following standardized cleaning tactics. This ensures consistency and promotes a culture of preventive protection.
In operations concerning both heat exchangers and vacuum pumps, the interdependence of those additives should be actually explained to technicians. Any problem inside the vacuum machine can directly have an effect on the thermal performance and lifespan of the warmth exchanger.
Encouraging Proactive Maintenance
Empowering operators to take ownership of protection obligations can result in faster problem identification and reduced downtime. Providing easy get entry to to tracking gear, statistics logs, and renovation manuals complements their capability to make knowledgeable choices. A proactive technique also encourages well timed replacements and allows prevent most important breakdowns.
Frequently Asked Questions (FAQs)
What is the pleasant manner to easy a C300 warmness exchanger?
The handiest cleansing approach relies upon at the form of fouling. Chemical cleansing is appropriate for mineral or organic buildup, at the same time as mechanical cleansing works for stable or sticky deposits. Clean-In-Place structures can simplify habitual renovation with out dismantling the unit.
How regularly should I investigate my C300 warmth exchanger?
Routine inspections have to be performed month-to-month or quarterly depending at the running surroundings. More frequent checks are advocated for structures dealing with corrosive fluids, excessive temperatures, or vacuum-assisted operations.
What effect do vacuum pumps have on warmness exchanger preservation?
Vacuum pumps can affect condensation stages and pressure dynamics inside a gadget. This can result in moisture intrusion, fouling, or corrosion if no longer well controlled. Monitoring these outcomes is vital for long-time period exchanger performance.
How can I enlarge the lifestyles of gaskets in a C300 heat exchanger?
To increase gasket lifestyles, keep away from fast temperature fluctuations, use well suited substances, and follow even torque at some point of installation. Periodic inspection for signs of wear or leakage will assist prevent unexpected screw ups.
What’s the common lifespan of a C300 warmth exchanger with proper maintenance?
With constant cleansing, tracking, and timely part replacement, a C300 warmth exchanger can remaining 15 to 20 years or greater. The lifespan may additionally range relying on utilization intensity and the nice of the fluids worried.